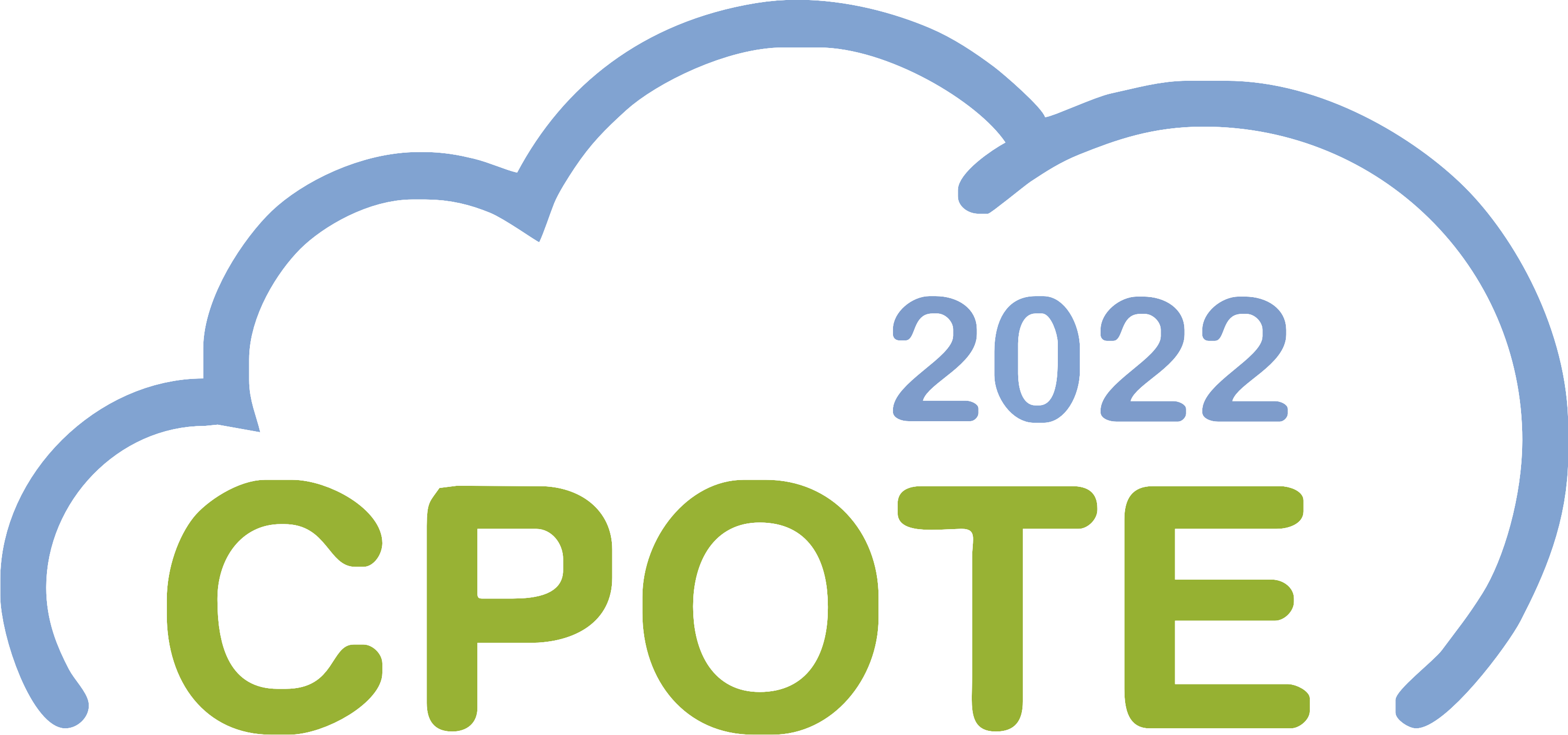
CPOTE2022
7th International Conference on
Contemporary Problems of Thermal Engineering
Hybrid event, Warsaw | 20-23 September 2022
7th International Conference on
Contemporary Problems of Thermal Engineering
Hybrid event, Warsaw | 20-23 September 2022
Abstract CPOTE2022-1129-A
Book of abstracts draft






Structural optimization of H-Rotor wind turbine blade combined based on one-way Fluid Structure Interaction approach
Łukasz MARZEC, Silesian University of Technology, PolandZbigniew BULIŃSKI, Silesian University of Technology, Poland
Tomasz KRYSIŃSKI, Silesian University of Technology, Poland
Jakub TUMIDAJSKI, Silesian University of Technology, Poland
In the last few decades vertical axis wind turbines (VAWTs) have gained
increased interest among researchers worldwide. This paper aims to present structural topology optimization of the H-Rotor wind turbines blade combined with one-way Fluid Structure Interaction (FSI) approach. The developed methodology couples the set of Unsteady Reynolds Averaged Navier-Stokes Equations (URANS) with the steady linear elasticity equations and density based topology optimization method to reduce the mass of the blades with respect to maximum stress and deformation limits. The obtained results provide detailed information on the unsteady flow fields around the operating wind turbine as well as optimized topology of blade interior without affecting the external aerodynamic profile. The load of pressure profile from CFD simulation was implemented at the point of rotation at which force values observed at blade surface were the highest. The centrifugal force was not neglected. Computations were carried out for the wind speed equal to 25 m/s and the tip speed ratio equal to 4. The parameters were to represent the extreme operating conditions. The simulations were performed using the commercial ANSYS software. The obtained results showed that the mass of blade, made of the same material, can be easily reduced by around 75% with the reduction of the observed stress values.
Keywords: Fluid structure interaction, Computational fluid dynamics (CFD), Finite element method, H-rotor wind turbine, Vertical axis wind turbine
Acknowledgment: The financial support of The National Science Centre, Poland, within OPUS scheme under contract 2017/27/B/ST8/02298 is gratefully acknowledged herewith