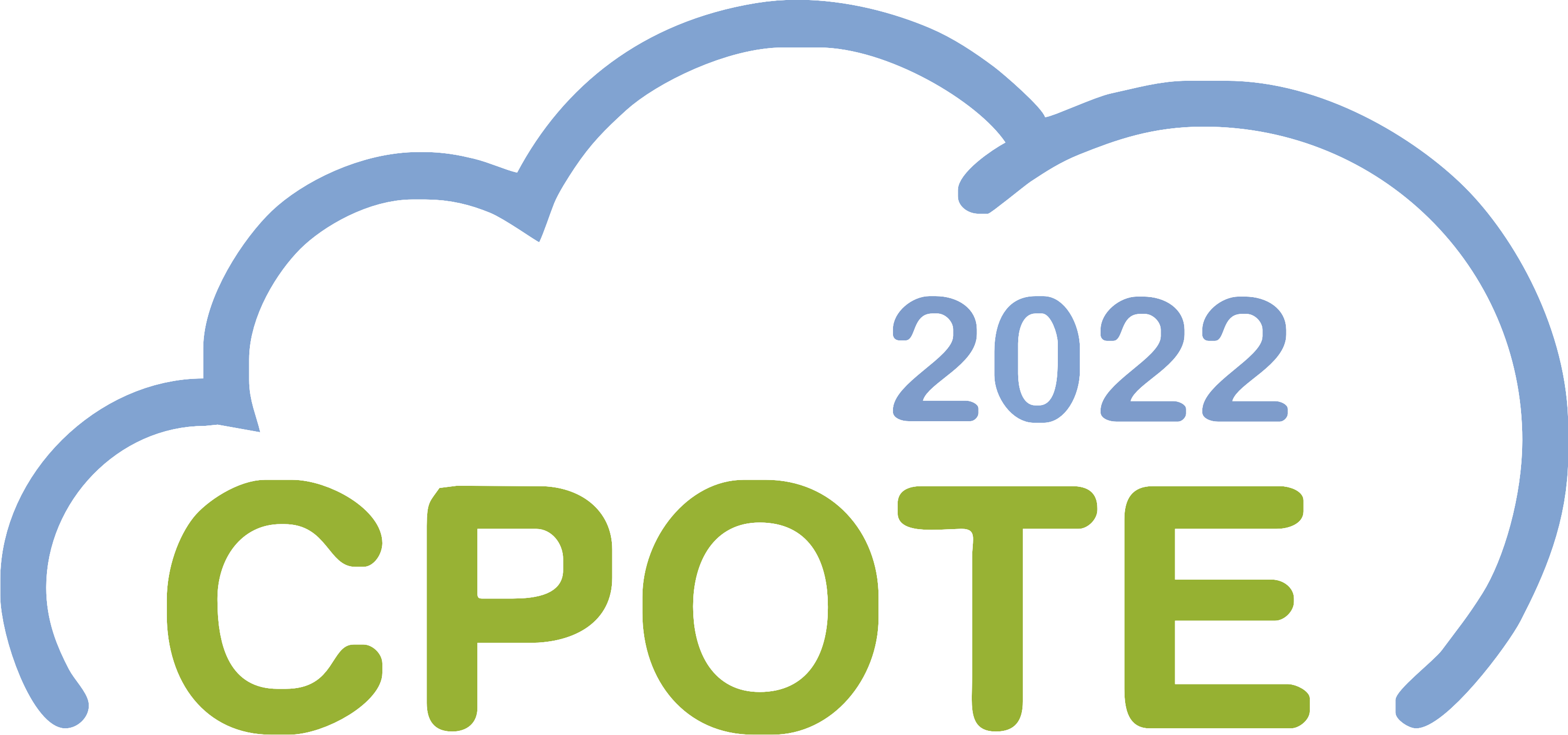
CPOTE2022
7th International Conference on
Contemporary Problems of Thermal Engineering
Hybrid event, Warsaw | 20-23 September 2022
7th International Conference on
Contemporary Problems of Thermal Engineering
Hybrid event, Warsaw | 20-23 September 2022
Abstract CPOTE2022-1126-A
Book of abstracts draft






Conceptual design of experimental test rig for research on thermo-flow processes during direct contact condensation in the two-phase Spray-Ejector Condenser
Paweł MADEJSKI, AGH University of Science and Technology, PolandMichał KARCH, AGH University of Science and Technology, Poland
Piotr MICHALAK, AGH University of Science and Technology, Poland
Krzysztof BANASIAK, Sintef Energy, Norway
The Carbon Capture Utilization and Storage (CCUS) technologies reduce greenhouse gas emissions, and one specific approach is combining CCUS with oxy-combustion power generation units. Oxygen is used for the combustion process instead of air, mainly to eliminate the nitrogen content in the flue gas, and it allows generating flue gas with carbon dioxide and water vapor as the major contents. The paper presents the conceptual design of a prototype experimental facility for mixing jet-type flow condensers investigations when the steam in exhaust gases is condensed on the water jet in the presence of CO2. The proposed experimental test rig was designed to give abilities to investigate the effectiveness of jet condensers experimentally as part of the CO2 capture phase and especially to investigate Spray-Ejector Condensers (SEC) developed as the combination of ejector and condenser devices. The paper presents the design and key features of the prototype installation components. The basic design was developed based on the simulation results, and for this purpose model of installation, including characteristics of individual components, was built. The developed model helps to evaluate the main performances of the conceptual test rig and supports the test-rig design process. The main components and the features of the steam generation unit, CO2 supply and mixing with steam, process water preparation, and H2O and CO2 separation subsystem are discussed. The measuring system was designed to test the efficiency of compression and condensation processes of the SEC fed by the CO2/H20 gas mixture.
Keywords: Two-phase ejector, Direct contact condensation, Design of experiment, Steam condensation, Oxy-combustion CO2 capture
Acknowledgment: The research leading to these results has received funding from the Norway Grants 2014-2021 via the National Centre for Research and Development. Work has been prepared within the frame of the project: "Negative CO2 emission gas power plant” - NOR/POLNORCCS/NEGATIVE-CO2-PP/0009/2019-00 which is co-financed by programme “Applied research” under the Norwegian Financial Mechanisms 2014-2021 POLNOR CCS 2019 - Development of CO2 capture solutions integrated in power and industry processes.